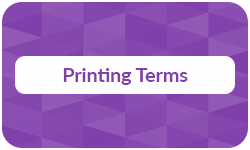
Printing is vital in sharing information, ideas, and creativity. To navigate the world of print effectively, it’s helpful to understand key terms used in the industry. This guide offers a clear overview of essential printing vocabulary, covering techniques, materials, tools, and historical references. Whether you’re a designer, student, or simply curious, these terms will help you better grasp the language of print.
Definition: Printing terms
Printing terms are words and phrases commonly used in the printing industry to describe processes, materials, tools, layouts, and techniques. They help professionals communicate clearly and ensure accuracy throughout the design and production stages.
Note: If you’re looking for a specific term, simply press Ctrl + F (or Cmd + F on Mac) to search for it quickly on this page.
Your guide to print and production
- Information on print finishing & print processing
- Information on materials & optimal use of materials
- Information on printing processes & print production
Learn more!
Printmaking
Printmaking refers to the full range of techniques used to produce printed images and text, from historic methods like woodcut and engraving to advanced digital and 3D printing. These processes influence the look, texture, and function of printed media across many formats.
Traditional techniques
Traditional techniques in printmaking rely on manual craftsmanship and centuries-old methods like engraving, woodcut, and etching. These forms laid the foundation for modern printing by shaping how images and text were first reproduced.
Aquatint
An etching technique creating tonal areas with resin.
Collagraph
Prints made from textured collages on a plate.
Engraving
Cutting designs into hard surfaces for printing.
Etching
Acid-carved lines in a metal plate for prints.
Intaglio printing
Printing from recessed lines or areas on a plate.
Letterpress printing
Relief printing with raised type or plates.
Linocut
Relief printing using carved linoleum blocks.
Lithography
Flat surface printing based on oil and water repulsion.
Planographic printing
Printing from a flat, chemically treated surface.
Relief printing
Printing from raised areas of a surface.
Screen printing
Ink pushed through a mesh stencil onto material.
Stencil printing
Applying ink through cut-out designs.
Woodcut
Relief prints carved from wood blocks.
Modern techniques
Modern techniques in printmaking use digital tools and advanced machinery to create precise, high-speed prints. From inkjet and laser printing to 3D and sublimation, these methods have revolutionized how we produce images and text today.
3D printing
Creating objects layer by layer from digital files.
Digital printing
Directly transferring digital images to paper or media.
Flexography printing
Rotational relief printing with flexible plates.
Gravure printing
Intaglio printing using engraved cylinders.
Inkjet printing
Spraying tiny ink droplets onto surfaces.
Large format printing
Producing oversized prints like banners and posters.
Laser printing
Electrostatic printing with toner and lasers.
Offset printing
Ink transferred from plate to rubber to paper.
Pad printing
Transferring ink with a silicone pad.
Sublimation printing
Heat-based transfer of dye into materials.
Thermal printing
Using heat to create images on special paper.
Print finishing
Print finishing includes all techniques applied after the printing process to improve the final product. These methods can enhance visual appeal, add functionality, protect the surface, or create custom effects tailored to specific purposes.
General finishing techniques
General finishing techniques cover a wide range of processes used to refine printed materials, whether by improving durability, adding texture, or creating a more polished, professional look.
Debossing
Pressing designs below the paper surface.
Die cutting
Cutting custom shapes into printed materials.
Edge painting
Coloring the edges of a printed item.
Embossing
Raising parts of the design into relief.
Perforating
Adding tearable lines or holes in paper.
Paper coating
Paper coating refers to surface treatments applied to printed materials to improve durability, enhance appearance, or create special tactile effects.
Aqueous coating
Water-based protective layer.
Glitter paint
Coating with reflective particles.
Lamination
Creates raised textured effects on the surface.
Relief paint
Creates raised textured effects on the surface.
Scratch-off printing
Coating that can be removed by scratching.
Textured paint
Paint that adds tactile surfaces.
UV coating
Glossy finish cured with ultraviolet light.
Varnish
Gloss or matte protective finish.
Foil stamping
Foil stamping is a decorative printing technique that uses heat and pressure to apply metallic or pigmented foil to a surface, adding visual flair and texture.
Cold foil stamping
Using adhesives to apply foil without heat.
Digital foil printing
Digital process of adding foil effects.
Holographic foil printing
Foil with rainbow or 3D holographic effects.
Hot foil stamping
Heat-based application of foil materials.
Printing inks
Printing ink encompasses all substances used to apply color and images to surfaces, from specialty security inks to standard pigments.
Ink types
Ink types refer to the various formulations of ink used across different printing methods. Each type is designed for specific surfaces, effects, or technologies, from water-based inks to metallic and UV-reactive options.
Discharge ink
Removes dye from fabric instead of adding color.
Dye ink
Color dissolved in liquid for vivid prints.
Fluorescent ink
Bright inks that glow under UV light.
Glow in the dark ink
Stores light and glows in darkness.
Invisible ink
Only visible under special conditions.
Magnetic ink
Contains particles readable by machines.
Metallic ink
Reflective ink with metal particles.
Oil-based ink
Ink using oil carriers for drying and adhesion.
Pigmented ink
Contains solid particles for color stability.
Plastisol ink
Plastic-based ink commonly used on textiles.
Reflective ink
Reflects light for high visibility.
Ribbon ink
Used in impact printers with inked ribbons.
Solid ink
Wax-based ink melted during printing.
Solvent ink
Uses chemical solvents for adhesion.
Sublimation ink
Becomes gas when heated for transfer printing.
Toner cartridge
Powdered pigment for laser printers.
UV ink
Cured instantly with ultraviolet light.
Water-based ink
Uses water as the primary solvent.
Printer paper
Printer paper refers to the wide range of materials used in printing, varying in weight, texture, coating, and format. These paper types are chosen based on print purpose, quality requirements, and compatibility with specific printers or ink types.
Printer paper types
Printer paper types describe the various kinds of paper available for different printing needs, ranging from standard office sheets to specialized textured or coated stocks.
Bond paper
Durable paper often used for documents.
Book paper
Paper commonly used for books and publications.
Coated paper
Paper with a smooth treated surface.
Copy paper
Standard white paper for office use.
Glossy paper
Shiny surface for vivid colors.
Inkjet paper
Optimized for inkjet printers.
Kraft paper
Durable brown paper for packaging.
Laid paper
Textured paper with visible lines.
Linen paper
Textured to look like linen fabric.
Matte paper
Non-reflective surface.
Metallic paper
Shimmery, reflective finish.
Mirror paper
Highly reflective surface.
Newsprint paper
Lightweight paper for newspapers.
Perforated paper
Pre-cut lines for easy tearing.
Photo paper
Special coating for photo printing.
Recycled paper
Made from recovered materials.
Resume paper
High-quality paper for resumes.
Satin paper
Soft sheen surface.
Seed paper
Contains plant seeds for planting.
Silk paper
Smooth, low-sheen finish.
Tracing paper
Transparent paper for drawing copies.
Uncoated paper
No surface treatment.
Vellum paper
Translucent, smooth paper.
Waterproof paper
Resistant to water damage.
Wove paper
Smooth, uniform surface.
Paper weight
Paper weight indicates the thickness and density of paper, which affects its feel, durability, and suitability for specific print jobs.
Caliper
Measurement of paper thickness.
Cardboard
Heavy-duty paperboard material.
Cardstock paper
Thick, stiff paper for covers or cards.
Cover stock
Heavy paper used for cover pages.
GSM
Grams per square meter, measures paper weight.
GSM in pounds
Conversion of GSM to pounds per ream.
Heavyweight paper
High-density paper stock.
Lightweight paper
Thinner, low-weight paper.
Paper thickness
Distance between the surfaces of a sheet.
Paperboard
Thick material used for packaging.
Paper size
Paper size refers to standardized dimensions of paper used around the world, including both international ISO formats and regional standards like U.S. Letter or Legal.
A0 paper dimensions | ISO A0 size measuring 841 × 1189 mm (33.1 × 46.8 inches). |
A1 paper dimensions | ISO A1 size measuring 594 × 841 mm (23.4 × 33.1 inches). |
A10 envelope dimensions | Envelope format for very small inserts (26 × 37 mm). |
A2 paper dimensions | ISO A2 size measuring 420 × 594 mm (16.5 × 23.4 inches). |
A3 paper dimensions | ISO A3 size measuring 297 × 420 mm (11.7 × 16.5 inches). |
A4 paper dimensions | ISO A4 size measuring 210 × 297 mm (8.3 × 11.7 inches). |
A5 paper dimensions | ISO A5 size measuring 148 × 210 mm (5.8 × 8.3 inches). |
A6 paper dimensions | ISO A6 size measuring 105 × 148 mm (4.1 × 5.8 inches). |
A7 paper dimensions | ISO A7 size measuring 74 × 105 mm (2.9 × 4.1 inches). |
A8 envelope dimensions | Envelope format measuring 52 × 74 mm (2.0 × 2.9 inches). |
A9 paper dimensions | ISO A9 size measuring 37 × 52 mm (1.5 × 2.0 inches). |
ANSI paper size | American National Standards Institute engineering paper series. |
Envelope sizes | Standard envelope dimensions used internationally for mailing. |
Paper size A series | ISO 216 A series standard, ranging from A0 to A10. |
Paper size B series | ISO 216 B series standard, often used for posters and books. |
Paper size C series | ISO 269 C series standard for envelopes matching A sizes. |
Paper size half letter | US size measuring 279 × 432 mm (11 × 17 inches). |
Paper size ledger | US size measuring 432 × 279 mm (17 × 11 inches). |
Paper size legal | US size measuring 216 × 356 mm (8.5 × 14 inches). |
Paper size letter | US size measuring 216 × 279 mm (8.5 × 11 inches). |
Paper size tabloid | US size measuring 279 × 432 mm (11 × 17 inches). |
US paper size | Standard paper formats, commonly used in the US and Canada. |
Types of printers
Printers come in many forms, each suited to specific tasks and technologies. This section covers the main types of printers used in homes, offices, and production environments.
Printer types
Printer types encompass a wide variety of printing machines used in home, office, and industrial settings. Each model is suited to different formats, speeds, and functions, from basic inkjet printers to high-end sublimation or 3D units.
A3 printer | Supports printing on A3 size paper. |
All-in-one printer | Combines printing, scanning, copying, and faxing. |
Barcode printer | Prints barcode labels and tags. |
Canvas printer | Prints directly onto canvas material. |
Color printer | Produces prints in full color. |
Continuous ink printer | Uses refillable ink tanks for high-volume printing. |
Digital printer | Receives data digitally to produce prints. |
Dot matrix printer | Impact printer using pins and ribbons. |
Duplex printer (and simplex) | Prints on both sides of the paper (duplex) or one side (simplex). |
Flatbed printer | Prints on flat surfaces or rigid media. |
Ink tank printer | Uses large ink reservoirs instead of cartridges. |
Inkjet printer | Sprays droplets of ink onto paper. |
Inkjet printer vs. laser printer | Comparison of inkjet and laser technologies. |
Label printer | Produces adhesive labels. |
Large format printer | Prints oversized materials such as posters. |
Laser printer | Uses toner and laser beams for high-speed output. |
LED printer | Similar to laser printers but uses LED arrays. |
Line printer | High-speed printer that prints a line at a time. |
Mobile printer | Portable printer for on-the-go use. |
Monochrome printer | Prints in black and white only. |
Multifunction printer | Performs multiple tasks like printing and scanning. |
Network printer | Shared printer connected to a network. |
Plotter | Produces vector graphics, often for engineering drawings. |
Portable printer | Compact, battery-powered printer. |
Poster printer | Prints large posters and banners. |
PVC card printer | Prints on plastic cards like IDs. |
Solid ink printer | Uses solid wax-based ink sticks. |
Sticker printer | Produces stickers and labels. |
Sublimation printer | Transfers dye into materials via heat. |
Thermal printer | Heat-sensitive printing, often for receipts. |
UV printer | Cures ink instantly with UV light. |
Print resolution
Print resolution describes the clarity and detail of printed images. It depends on how data is measured and rendered by devices.
Resolution terms
Resolution terms describe the level of detail and clarity in printed images. Understanding units like DPI and PPI is essential for ensuring high-quality, sharp print output across different media.
DPI | Dots per inch; measures print resolution. |
Megapixel | One million pixels; measures image resolution. |
Pixel | Smallest unit of a digital image. |
PPI | Pixels per inch; measures screen or digital resolution. |
Vector image | Graphics made of paths and shapes, scalable without quality loss. |
Paper folding
Paper folding techniques are used to shape printed sheets into structured formats like brochures, mailers, or product inserts. Each fold type affects layout, navigation, and how information is visually delivered to the reader.
Folding styles
Folding styles are the standard ways printed sheets are folded during production. These formats affect layout, readability, and how printed pieces like brochures or mailers function.
Accordion fold
Zig-zag folding into multiple panels.
C fold
Tri-fold with panels folded inward.
Double parallel fold
Folded in half, then in half again in same direction.
French fold
Folded twice perpendicular to each other.
Gate fold
Panels that open to reveal content inside.
Half fold
Single fold down the center.
Roll fold
Each panel folds in over the previous.
Tri fold
Divides sheet into three equal parts.
Print color
Print color covers the use of color models, systems, and reproduction techniques to ensure accurate and consistent results. It includes both technical aspects, like RGB or CMYK, and visual concepts such as hue, saturation, and tone.
Color concepts
Color concepts cover the fundamental principles of how color is defined, mixed, and reproduced in print. From color models to saturation and gamut, these terms help ensure color accuracy across devices and materials.
Additive colors
Colors created by combining light sources (e.g., RGB).
Color cast
An unwanted overall tint in an image or print.
Color correction
Adjusting colors to achieve accurate reproduction.
Color depth
The number of bits used to describe color in a pixel.
Color gamut
The full range of colors that a device can reproduce.
Color gradient
A smooth transition between two or more colors.
Color hue
The attribute that defines a pure color (e.g., red, blue, yellow).
Color mixing
Combining colors to create new hues or shades.
Color model
A mathematical system describing how colors are represented (e.g., RGB).
Color space
A specific implementation of a color model defining a range of colors.
Color tone
The lightness or darkness of a color.
Hex code
A six-digit alphanumeric code representing a specific color digitally.
ICC profile
Data describing how a device reproduces color for consistent output.
Metamerism
When colors look the same under some lighting but different under others.
Pigment
A coloured substance used in ink or paint to create color.
Saturation color
The intensity or purity of a color.
Subtractive colors
Colors created by combining pigments or dyes (e.g., CMY/CMYK).
Color systems
Color systems are standardized ways to define and reproduce colors across different devices and media, ensuring visual consistency in design and printing.
CMY
Cyan, magenta, yellow subtractive model.
CMYK
Cyan, magenta, yellow, black subtractive model.
HSL
Hue, saturation, lightness model.
HSLA colors
HSL model with alpha transparency.
HSV colors
Hue, saturation, value model.
Munsell color system
Defines colors by hue, value, and chroma.
Pantone colors
Standardized color matching system.
RAL
European color matching system.
RGB
Red, green, blue additive color model.
RYB
Red, yellow, blue traditional model.
Bookbinding
Bookbinding is the process of assembling printed pages into a finished book using specific tools, techniques, and materials. It enhances durability, usability, and presentation, ranging from simple softcover formats to elaborate hardcover bindings.
Binding components
Binding components are the individual parts that make up a bound book, such as the spine, cover, and endpapers. These elements affect both the structure and usability of printed books.
Book block
Main body of a book's pages.
Book corners
Reinforcements applied to book corners.
Book cover
Outer protective covering of a book.
Book rebinding
Repairing or replacing existing bindings.
Book spine
Edge that holds pages together.
Endpaper
Sheet connecting the book block to the cover.
Fore edge
Outer edge opposite the spine.
Ribbon marker
Fabric bookmark sewn into the spine.
Bookbinding materials
Bookbinding materials are the fabrics, adhesives, and reinforcements used to construct and hold books together during the binding process.
Book cloth
Fabric used to cover the book board.
Bookbinding glue
Adhesive for securing pages and covers.
Buckram
Durable cloth for book covers.
Gauze
Mesh reinforcing the book spine.
Muslin
Cotton cloth liner used in binding.
Book boards
Book boards are rigid panels that form the core structure of hardcovers, giving books their shape, strength, and protection.
Bristol board
Smooth, stiff paperboard.
Chipboard
Recycled fibre board for covers.
Davey board
High-grade bookbinding board.
Greyboard
Thick, gray recycled board.
Museum board
Archival-quality board for preservation.
Bookbinding tools
Bookbinding tools are the specialized instruments used in assembling, binding, and finishing books by hand or in small-batch production.
Awl
Pointed tool for piercing holes.
Book press
Compresses books for binding.
Folding bone
Tool for creasing and folding paper.
Paper drill
Drills holes through paper stacks.
Bookbinding types
Bookbinding types refer to the various ways books are constructed and bound, from rigid hardcover editions to flexible paperback formats.
What is hardcover
Rigid-bound book cover.
What is softcover
Flexible paper cover.
What is paperback
Softcover bound book.
Miscellaneous printing terms
Printing involves countless details, from specialized tools to design principles and production processes. This section gathers additional terms you may encounter in any aspect of printing and publishing.
Layout & design
Layout and design covers visual elements and formatting principles used to organize printed content, enhance readability, and support aesthetic appeal.
ASCII
A basic text format made of characters and symbols.
Bookplate
Decorative label identifying the book owner.
Contrast
Difference between light and dark areas.
Crop marks
Lines showing where to trim a print.
Dog ear
Folded corner of a page.
Golden ratio
Ideal proportion, often used in design.
Indicia
Postal info printed on bulk mail.
ISBN
Unique identifier number for books.
Landscape format
Horizontal page orientation.
Logotype
A text-based logo design.
Opacity
How see-through an element is.
Portrait format
Vertical page orientation.
Raster
Pixel-based image made of a grid.
Scaling
Resizing an image or object up or down.
Historical & cultural
Historical and cultural printing terms relate to the origins, traditions, and evolution of print media and book production throughout history.
Ex libris
A label indicating the owner of a book.
Facsimile
An exact copy or reproduction of a document.
Imprimatur
Formal approval to print a work, often from an authority.
Incunabulum
Books printed before the year 1501.
Johannes Gutenberg
Inventor of the first movable-type printing press.
Lorem ipsum
Placeholder text used in design layouts.
Papyrus
Early paper-like material used in ancient writing.
Materials & components
Materials and components refer to the physical elements involved in printing and binding, including types of paper, sheets, and structural materials.
Cover stock
Thicker paper used for covers.
Deckle edge
Rough, untrimmed edge of paper.
Interleaves
Extra sheets placed between printed pages.
Paper stock
The base paper used for printing.
Ream
A standard pack of 500 sheets of paper.
Print techniques & effects
Print techniques and effects describe various artistic and functional methods used to produce visual outcomes, textures, and finishes in printed work.
Airbrush
Smooth, sprayed-on color effect.
Black and white
Printing using only black ink.
Blind embossing
Raised design without using ink or foil.
Blueprint
A detailed reproduction of technical drawings.
Die-cut
Custom-cut shape or pattern in printed material.
Dithering
Technique to simulate gradients with small dots.
Grayscale
Image made of shades of gray, without color.
Moiré pattern
Visual distortion caused by overlapping patterns.
Monochrome
Printing in one single color or tone.
Watermark
Faint image or text embedded in the paper for copyright.
Printing hardware & prepress
Printing hardware and prepress include essential tools and processes used before and during printing, from preparing plates to assembling printed pages.
CDD (Charge-coupled device)
Sensor used in scanners.
Collate
To assemble printed pages in the correct order.
Densitomete
Tool to measure ink density on prints.
Prepress
All steps before the actual printing begins.
Printhead
Part of a printer that applies ink.
Printing plate
Surface used to transfer ink to paper.
Thread counter
Magnifying tool for checking fine print details.
Printing services at BachelorPrint
- Individual solutions & personal support
- High print quality & fast production times
- Wide range of print products for every need
Learn more!
FAQs
Printing terms are industry-specific words that describe materials, techniques, tools, and processes used in printing and design.
Grayscale uses different shades of gray, while monochrome means one single color (usually black or another solid tone).
“Lorem ipsum” is used as placeholder text to focus on layout and design without being distracted by actual content.
The main methods are: Offset, digital, flexography, gravure, screen, 3D, letterpress, and inkjet printing.